Plastometrex is a technology company based in Cambridge, and our technology is based on over a decade’s worth of published scientific research work. Our roots are academic ones, and we have a long and distinguished academic track record. In fact, our Chief Scientific officer, Professor Bill Clyne, is an Emeritus Professor at the University of Cambridge, and our core scientific team are all former PhD students from his group. Those scientific credentials continue to be felt in and around the company, and we continue to support and encourage academic collaborations having already established relationships with a number of UK universities. Another exciting collaboration is now underway, this time with our friends and colleagues from the Worcester Polytechnic Institute (WPI) – a private research university in Worcester, Massachusetts, which has graduate degree programs in science, engineering, and technology.
Assistant Professor, Dr. Danielle Cote, from the Materials Science and Engineering program has research interests in computational thermodynamic and kinetic modelling, rapidly solidified (non-equilibrium) alloys, solid state additive manufacturing, and cold spray processing and characterisation. Dr. Cote also has additional research interests in developing databases to aid in integrated computational materials science and Dr. Cote established, therefore, the Centre for Materials Processing Data (CMPD) – an initiative in which members generate (and manage) time- and temperature-dependent material property data that can be used in process modelling and simulation. .
The activities taking place in Dr. Cote’s research group are closely aligned with our own personal research interests, but importantly they’re also well aligned with the capabilities and outputs of our Indentation Plastometer. Our technology can be used, for example, to measure metal strength parameters in a way that is simpler, quicker and more versatile than conventional mechanical testing methods. The test is simple in execution (and fully automated) and involves the creation of a small indent in the surface of a specimen. The residual profile shape is measured and then analysed in our custom-written software package which calculates and returns a full stress-strain curve – the entire process takes under 3 minutes.
One further advantage of the technology is that it can be used on very small test specimens, which is often all that’s available to institutes and organisations involved in activities around rapid alloy development and accelerated material discovery – as is the case at WPI. Having access to research tools that can support investigations into microstructure-processing-property relationship and/or in the validation and verification of theoretical strength models will be a key enabler in much of the work being done in Dr. Cote’s research group over the next few decades. The entire team at Plastometrex simply cannot wait to support these ambitious and exciting research activities, and we look forward to delivering the Indentation Plastometer to Dr. Cote and the WPI in June 2021.
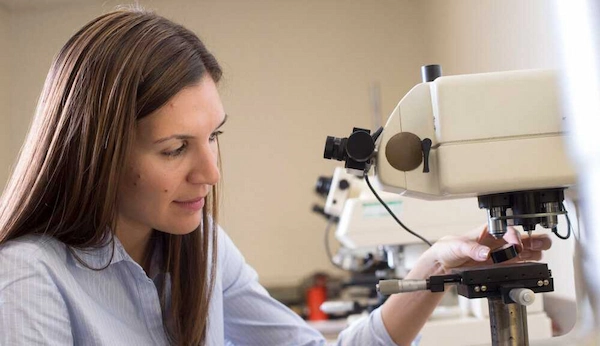
"Having the Indentation Plastometer allows us to significantly reduce the sample size required, not only saving time and material resources, but allowing us to generate mechanical data which we have yet to see on our materials."
Dr Daneille Coto, Assistant Professor at WPI