The University of Bolton is home to the UK’s only National Centre for Motorsport Engineering (NCME). It is an impressive £13 million state-of-the-art education facility that gives its students exposure to all elements of the engineering lifecycle, from product design to final testing.
The centre combines high-quality teaching curricula with hands-on practical modules that utilise the latest technologies, including metal additive manufacturing systems. This industry-led approach aims to develop high value and highly employable skill-sets for its students and researchers, propelling them onto successful careers in motorsport engineering and beyond.
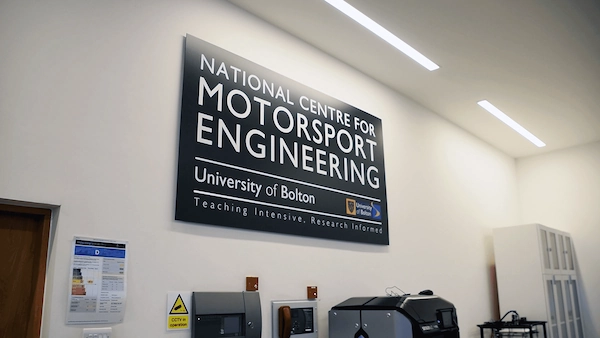
As part of its innovation drive, the NCME has recently acquired an Indentation Plastometer from Plastometrex. The novel mechanical testing device harnesses advanced numerical methods to measure metal strength parameters from a rapid and simple 3-minute test. The fast and automated nature of technology makes it an ideal tool for teaching, as it allows students to get hands-on and to run actual mechanical tests themselves. This empowers students to observe how manufacturing methods and processes impact the strength of engineering materials and components in real-time.
Prof. Bill Clyne, Chief Scientific Officer had this to say:
“Much of our team has deep academic roots and as a company we are genuinely passionate about supporting educators, students and researchers. We are delighted to be working with The National Centre of Automotive Engineering, a much-needed initiative that is focused on developing real engineering capability in its students.”
The Indentation Plastometer will also be used by NCME as a key research tool in the area of metal additive manufacturing. Specifically, the technology will support parameter and material development for metals printed via powder bed fusion. Conventional testing of printed parts is slow and expensive, often requiring machining operations and large volumes of material. It is common for this testing “bottleneck” to be the rate limiting step when developing new alloys or processes.
The Indentation Plastometer reduces this testing turnaround time from days to just 3-minutes. This will allow the research team at NCME to rapidly move through design space, and to develop and optimise new materials and manufacturing parameters far faster than before.
In addition to being quick and easy, PIP testing allows the study of anisotropy (properties in a particular location varying with direction) and inhomogeneity (properties varying with location). Both of these can be present in Additively Manufactured components and cannot readily be studied via conventional testing.
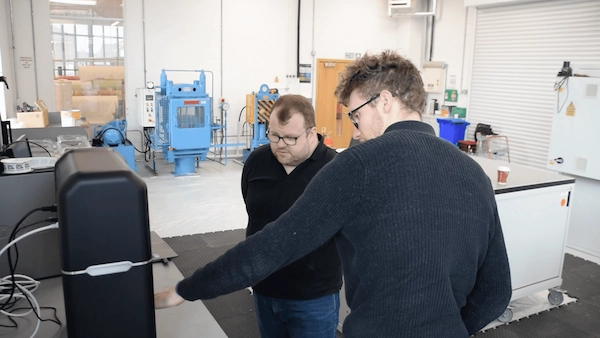
Robert Higham, Senior Lecturer at NCME had this to say about the technology:
“The development of efficient and accurate testing methods is a key enabler for the continued adoption of additive manufacturing. The Indentation Plastometer is a powerful new tool that will allow the community to develop and qualify parts far faster than before. We are excited to be working with the Plastometrex team to integrate their novel technology into both our teaching and research”