Plastometrex is a technology company formed by a team of materials scientists, all formerly of the University of Cambridge. The company combines advanced numerical methods with novel hardware systems to create new and revolutionary mechanical testing methods and products. Plastometrex's flagship product, the benchtop Indentation Plastometer, is a mechanical test device that extracts accurate metal stress/strain curves from a 3-minute indentation test. Since launching in 2020, the technology is already being used by leading companies and universities across the world, including Element Materials Technology and The University of Oxford.
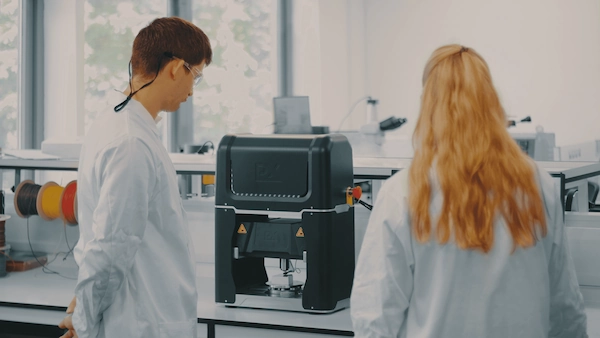
Plastometrex is now pleased to announce a new technical collaboration with Ovako, one of Europe's leading manufacturers of engineering steel. Ovako's steel carries an 80% lower carbon footprint than the global average. A feat that has been achieved through a unique combination of a scrap steel-based production process and a low-carbon electricity source mix. Ovako uses a sustainable manufacturing process to produce a range of engineering steels, including the bearing applications and manufacturing and transportation markets.
The two companies have formed a technical collaboration to extend the capabilities of the Indentation Plastometer to rapidly test the mechanical properties of very hard metals. Testing Ovako's recently launched Hybrid Steel® is a particular focus of the collaborative efforts. The novel grade results from the first successful combination of two well-established precipitation strengthening mechanisms – i.e. simultaneous hardening by both carbides and intermetallic precipitations. Hybrid Steel® is designed to meet the demands of high-stress, elevated-temperature applications where mechanical strength is critical.
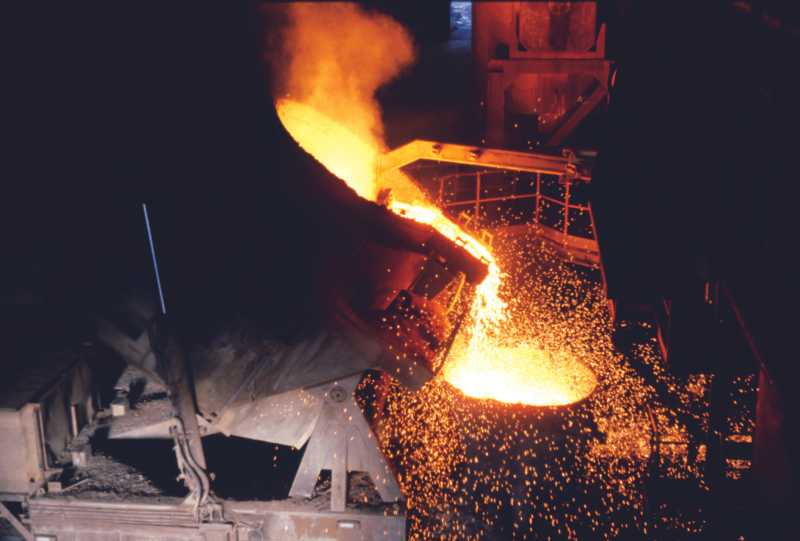
Ovako combine the use of scrap metal and a green energy mix to reduce the carbon footprint of their steel products
“We are very excited to be working closely with the Plastometrex team. Their platform methodology and innovative product provide a much-needed tool for both metallurgy R&D and production activities. By extending the capability of the technology to test the hardest metals, we will be able to use the technology to rapidly characterize and optimize our products as well as the novel Hybrid Steels.
Patrik Olund, Vice President and Head of Group R&D of Ovako, said.
Off the back of the Ovako collaboration, Plastometrex will shortly be releasing a new product update that will extend the maximum yield strength of testable materials. This will enable the device to test the vast majority of very hard engineering metals. Historically, it has been challenging to test the plasticity of these materials, owing to the high loads required from test equipment and the brittle nature of the materials when under tension. Plastometrex’s new product update will provide a rapid and accurate method for characterizing such materials, creating a valuable tool for both R&D and quality assurance activities.
Chief Scientific Officer, Professor Bill Clyne, who leads Plastometrex's research and development activities, had this to say about the collaboration:
We are extremely pleased with the technical collaboration with Ovako. They are a company with excellent scientific capabilities and a forward-thinking approach. Our collaborative work has been highly fruitful and directly resulted in capability improvements to our flagship product, which will soon be able to test very hard metals. We look forward to continuing to work with Ovako to push the frontiers of mechanical testing.
If you'd like to learn more about how PIP testing extracts stress/strain curves from indentation test data, get in touch with the Plastometrex team below.