In the realm of failure analysis and materials engineering, accurately understanding material properties is paramount. Traditionally, hardness testing has been a go-to method due to its convenience and cost-effectiveness. However, this approach presents limitations, particularly when detailed stress-strain relationships are required. This blog post delves into a case study exploring PIP as an insightful alternative to hardness numbers. Conducted in collaboration with the Health and Safety Executive Science Division, this study compares the efficacy of hardness, PIP, and tensile testing in providing comprehensive material insights.
The Challenge with Hardness Testing
Hardness testing, though widely used, is not without its drawbacks. It offers a single hardness number, which is not a fundamental material property. This number is often converted into ultimate tensile strength (UTS) or yield stress values through empirical relationships, but these conversions come with significant uncertainties and limitations. The BS EN ISO 18265:2013 standard, for instance, highlights that conversions involve considerable scatter and systematic errors, limiting their applicability to specific alloys. Moreover, hardness numbers do not provide full stress-strain curves, hindering accurate finite element modelling and detailed material behaviour analysis.
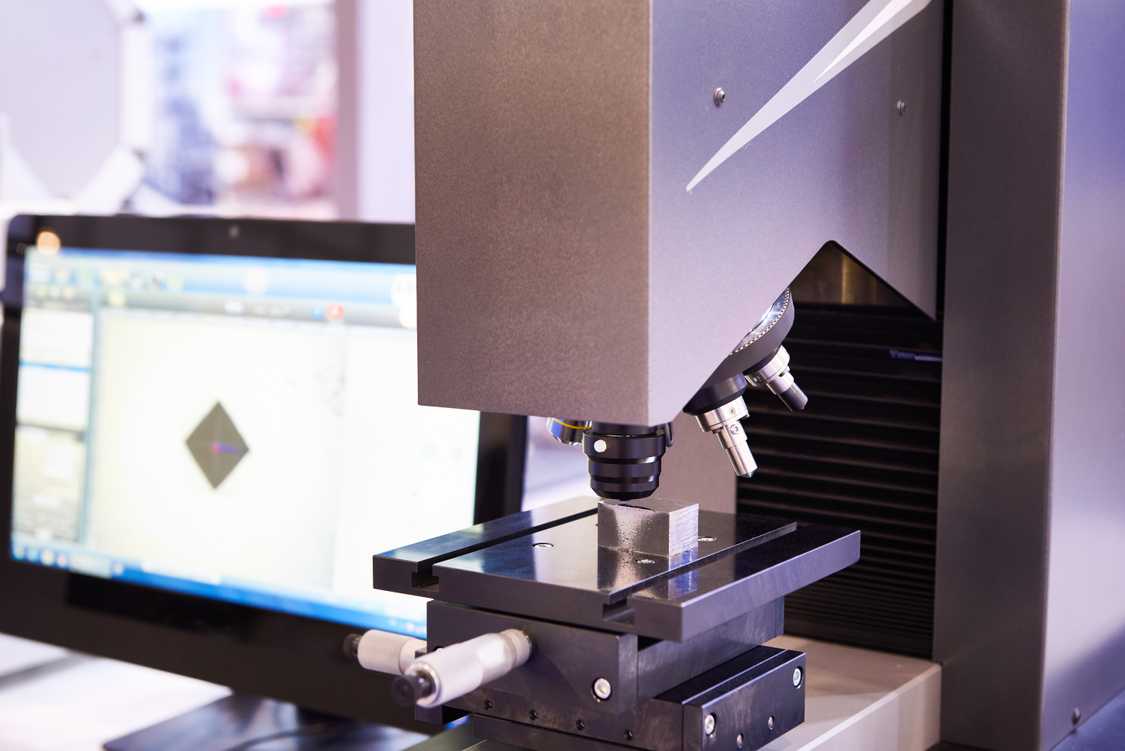
Objectives of the Study
The primary objective of this case study was to assess whether PIP testing could overcome the limitations of hardness testing and offer a more insightful understanding of material failure. The study aimed to evaluate the mechanical properties and stress-strain relationships of various metals using PIP, hardness, and tensile testing. Tensile testing, while considered the benchmark, requires larger, machined samples, making it less feasible for certain applications. PIP testing, on the other hand, promises the convenience of hardness testing while providing full stress-strain curves akin to tensile tests.
Methodology
The study involved 12 different materials, including Waspaloy, Aluminum 7075, Martensitic Steel, and several others. Tensile specimens were tested using an Instron 3369 loading frame, while PIP testing was performed using a PLX-Benchtop device. Hardness testing employed a Buehler Wilson VH3300 automatic Vickers hardness tester. PIP testing uses an accelerated inverse finite element method to infer accurate stress-strain curves from indentation data, offering a significant advantage over hardness testing's single-number output.
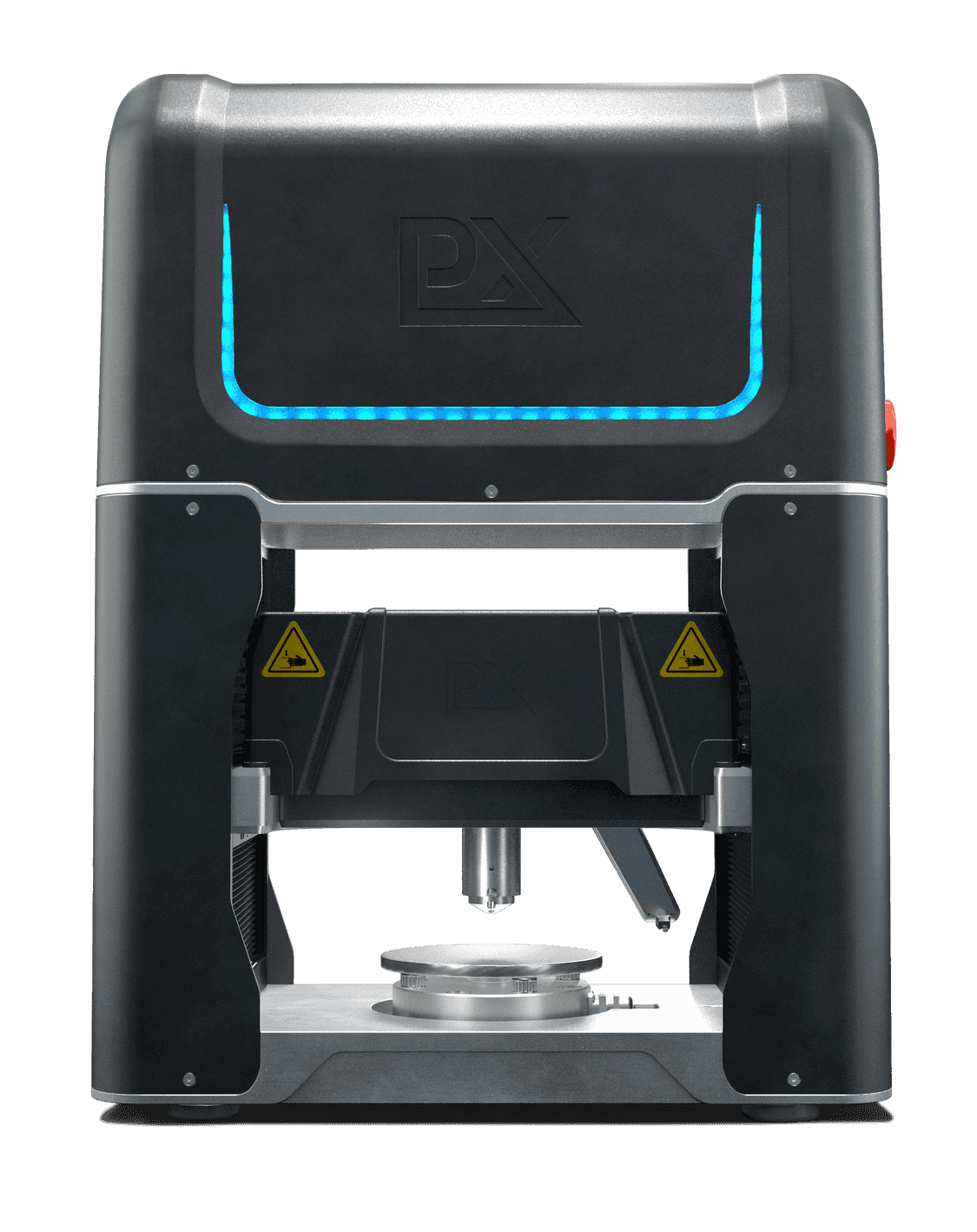
Results
The results revealed that PIP testing could indeed provide comprehensive stress-strain curves, including yield stress and hardening behaviour, which hardness testing could not. When comparing UTS values derived from hardness conversions and PIP testing against tensile test results, PIP showed a mean absolute percentage error of 3.8%, significantly lower than the 6.8% error from hardness testing. This demonstrated PIP's closer alignment with tensile testing and its ability to offer more reliable material insights.
Discussion and Outcomes
The study underscores that while hardness testing can serve as a complementary technique, it should be used with caution due to its limitations. PIP testing, however, provides detailed quantitative information and higher confidence levels in yield stress and UTS values. This makes it a valuable tool for failure analysis, especially when finite element modelling is required to predict and mitigate potential failures.
Conclusion
For failure analysis and materials engineers, adopting PIP testing presents a promising alternative to traditional hardness testing. By delivering full stress-strain curves and reducing uncertainties associated with empirical conversions, PIP testing enhances the accuracy and reliability of material property assessments. As the field continues to evolve, incorporating advanced techniques like PIP will be crucial in advancing our understanding and prevention of material failures.
Read the full case study here.