In this blog post, we explore how the PLX-Portable, a new device that uses PIP testing to non-destructively extract stress-strain curves, helps pipeline operators meet the PHMSA Mega Rule's material property testing requirements quickly and easily.
Background
Conformance with PHMSA’s “Mega Rule” centers on thorough application of risk-based integrity assessments. Recent publication of the final “Mega Rule” set further into motion a series of regulatory expectations which increase the scope and scale of the requirement to accurately measure and record the material properties of applicable oil and gas transmission pipelines.
While the legislation would see project owners and asset managers benefiting from a clearer, more informed view of the status of their assets, the availability of technology and processes that satisfy Mega Rule requirements has faced some challenges. Bottlenecks, regulatory hurdles, and a struggle to deploy commercially viable and scalable technologies have been a cause for concern. With a requirement of 50% of MAOP verification to be completed by mid-2028, the race is on!
This leads us to PIP testing. Already heavily validated, PIP is designed to extract accurate stress-strain curves from indentation test data. Based on a scientific methodology referred to as Indentation Plastometry, the evolution of PIP testing from academia to industry can be tracked through dozens of case studies and scientific publications, including those covering the testing of case-hardened layers and large, inhomogeneous aluminum forgings. Accuracy and insightful data are two key aspects of PIP testing, but that’s not all – PIP testing is also very quick!
“The focus is on developing a system that is accurate, quick and easy to deploy (single-person use), requires minimal training to use, and is scalable commercially"
Change, however, can be difficult. New innovations, justifiably, should be studied carefully and validated thoroughly, ensuring their ability to stand up under rigorous use in material property testing environments. In this case, however, it may be worth the effort, as pipeline operators (and those with past PMI and non-destructive testing experience) will relate to the need to employ novel technologies that are accurate, reliable, and suitable for meeting the scale of the challenge – a need that many have so far found difficult to satisfy.
With a benchtop PIP testing device commercially available and already in use providing faster, more cost-effective, and more insightful lab-based materials properties testing worldwide, we have now turned our focus to a new, portable version of the technology which is being developed specifically to address the Mega Rule challenges. The focus is on developing a system that is accurate, quick and easy to deploy (single person use), requires minimal training to use, and is scalable commercially. The system will also link to a cloud-based digital platform for TVC compliant record keeping.
PIP Testing
Uniaxial tensile testing has not changed much in over 100 years, despite some major limitations. In fact, in a survey of more than 450 manufacturing companies conducted by Plastometrex, 45% of the respondents selected tensile testing turnaround times as being the biggest bottleneck in the smooth running of their businesses. That is because tensile testing can be cumbersome and time-consuming, and it usually requires access to large volumes of material.
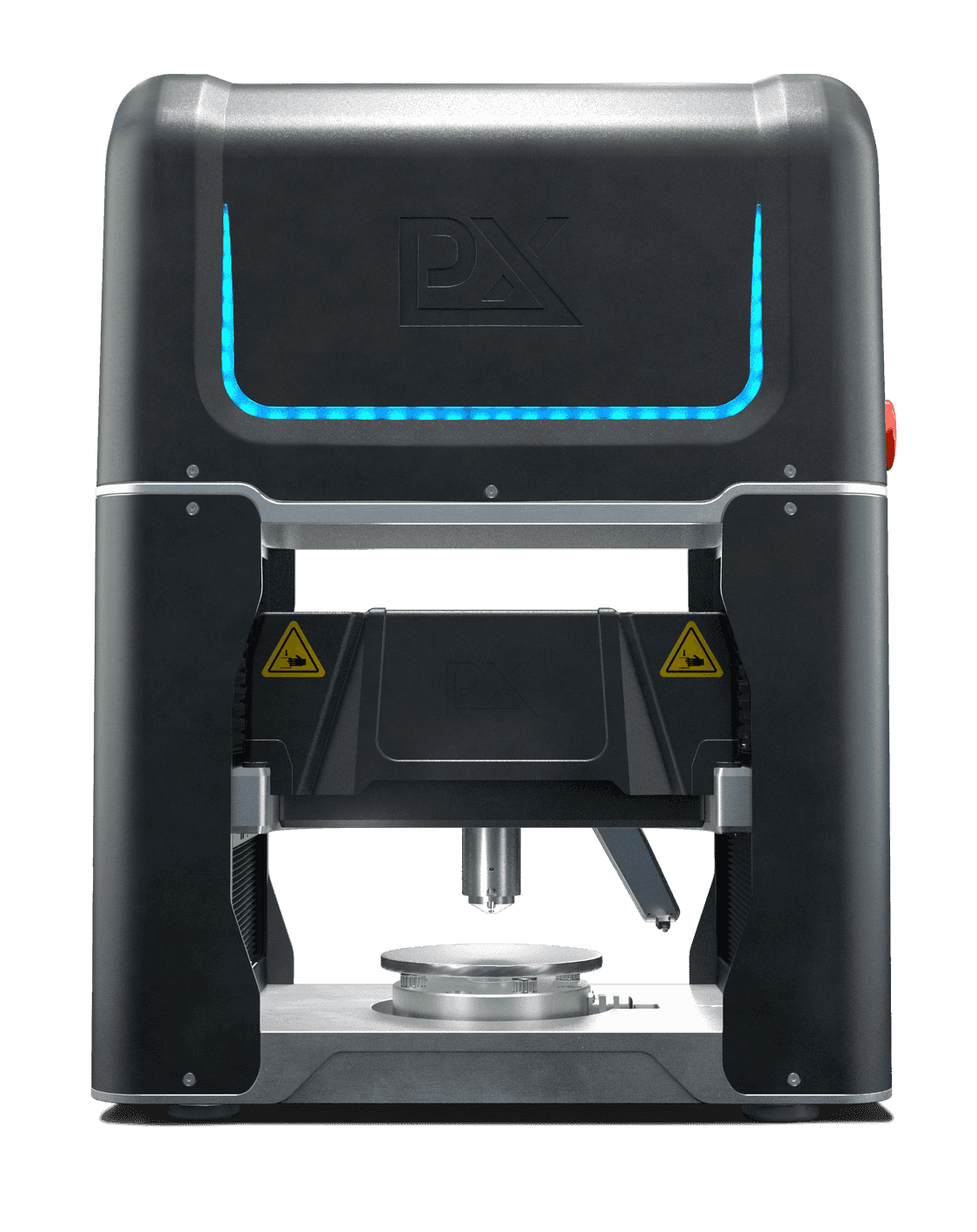
‍
Enter PIP testing—a technology developed and validated primarily through lab-based tests comparing PIP outcomes with results from conventional tensile tests by Plastometrex—but, and perhaps more convincingly, in collaboration with some of the world’s largest technology companies and some of the world’s most prestigious academic institutes.
In its simplest form, PIP testing involves the following sequence: creation of an indent by applying a load to an indenter head; measurement of the indent shape using an integrated stylus profilometer; finite element modeling of the indent procedure and iterative modification of the parameters in a constitutive plasticity equation; optimization towards convergence of modeled and experimental profile shapes; and determination of the underlying stress-strain behavior.
As for its history, Professor Bill Clyne, Chief Scientific Officer at Plastometrex, had initially stepped up to meet the challenge of reliable conversion of indentation test data, in the form of load-displacement curves or residual indent profiles, into full stress-strain curves, almost 20 years ago. Plastometrex has raised over ÂŁ6 million in venture capital and UK government funding to commercialize PIP testing technology with a mission of making mechanical testing simpler, faster, more versatile, and more insightful.
The Indentation Plastometer (Fig.1) emerged in late 2020. It is a benchtop macro-mechanical testing device that measures metal strength parameters (stress-strain curves) from a quick and simple indentation test. Its development and validation have been supported through collaborations with organizations including Ovako, the Welding Institute (TWI), the National Physical Laboratory (NPL), Oxford University, and Desktop Metal.
‍
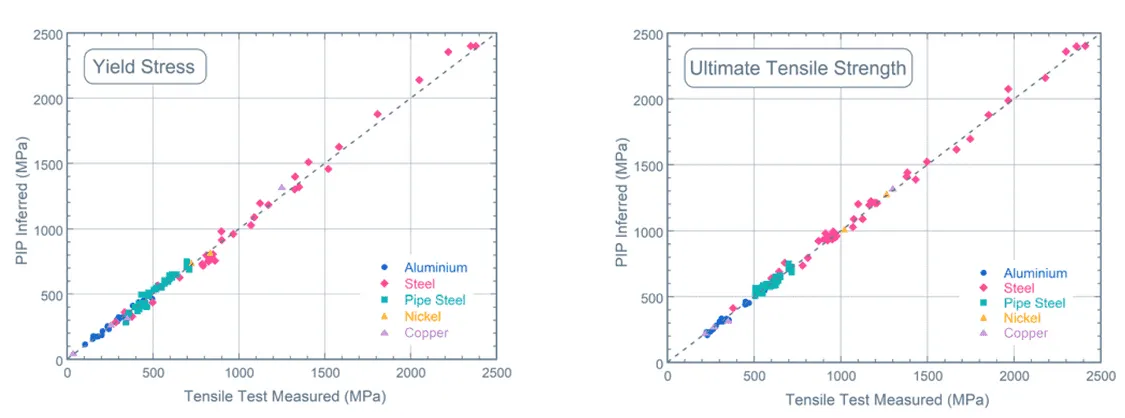
‍
In addition, and following their own technical due diligence, the testing, inspection, and certification giant - Element Materials Technology - took its own stake in the business. Machines are now in use at sites all over the world, including MIT, FIU, the Worcester Polytechnic Institute, and Oxford University.
PIP Testing in Action
PIP testing enables the testing of real components with minimal sample preparation required. It is used for a diverse range of applications, such as small-scale testing of novel aerospace alloys, high throughput testing in combinatorial alloy design, forensic failure analyses, the structural characterization of additively manufactured metals, and spatial mapping of property changes across welds, among others. Examples of validation data (Fig. 2) are available for the yield stress and ultimate tensile strength of a range of common engineering metals.
Fully integrated and fully automated, the technology allows users to switch from conventional mechanical testing to a process that can measure full tensile stress-strain curves and metal strength parameters in just a few minutes. The technology has been developed to reduce testing costs and testing turnaround times, and to help eliminate the lack of versatility that is the hallmark of conventional tensile testing.
In-Ditch Launch
Building on the success of the benchtop device, the Portable Indentation Plastometer, arriving summer 2023, is being designed and constructed for in-field testing of high-value metal assets in support of positive material identification, in-situ monitoring of material degradation over time, and asset and component life extension calculations.
“The portable PIP testing system is a direct derivative of the benchtop system, deployed in a different testing configuration, but employing the same proven scientific methodology.”
The full technical specification for the portable equipment (Fig. 3) has been developed in consultation with asset integrity service providers including ROSEN, Mistras, Acuren, DNV, RSI pipelines, and Element Materials Technology. What emerged from those discussions was, quite naturally, a requirement for the system to be accurate, but also a requirement for the system to be easier and faster to use than any of the current in-ditch testing technologies.
The system is single-person use, with user-guided workflows designed to make the operating steps involved with testing metal pipes as simple as possible. These steps include preparation of the pipe surface—typically involving a surface grinding operation using hand-held, off-the-shelf tools. Once the surface has been adequately prepared, a cradle is attached to the pipe using a bespoke strap-tightening system. The handheld indenter module is then attached to the cradle which houses power and electrical connections. Once the indent has been created, the indenter module is detached and the profilometer module is attached.
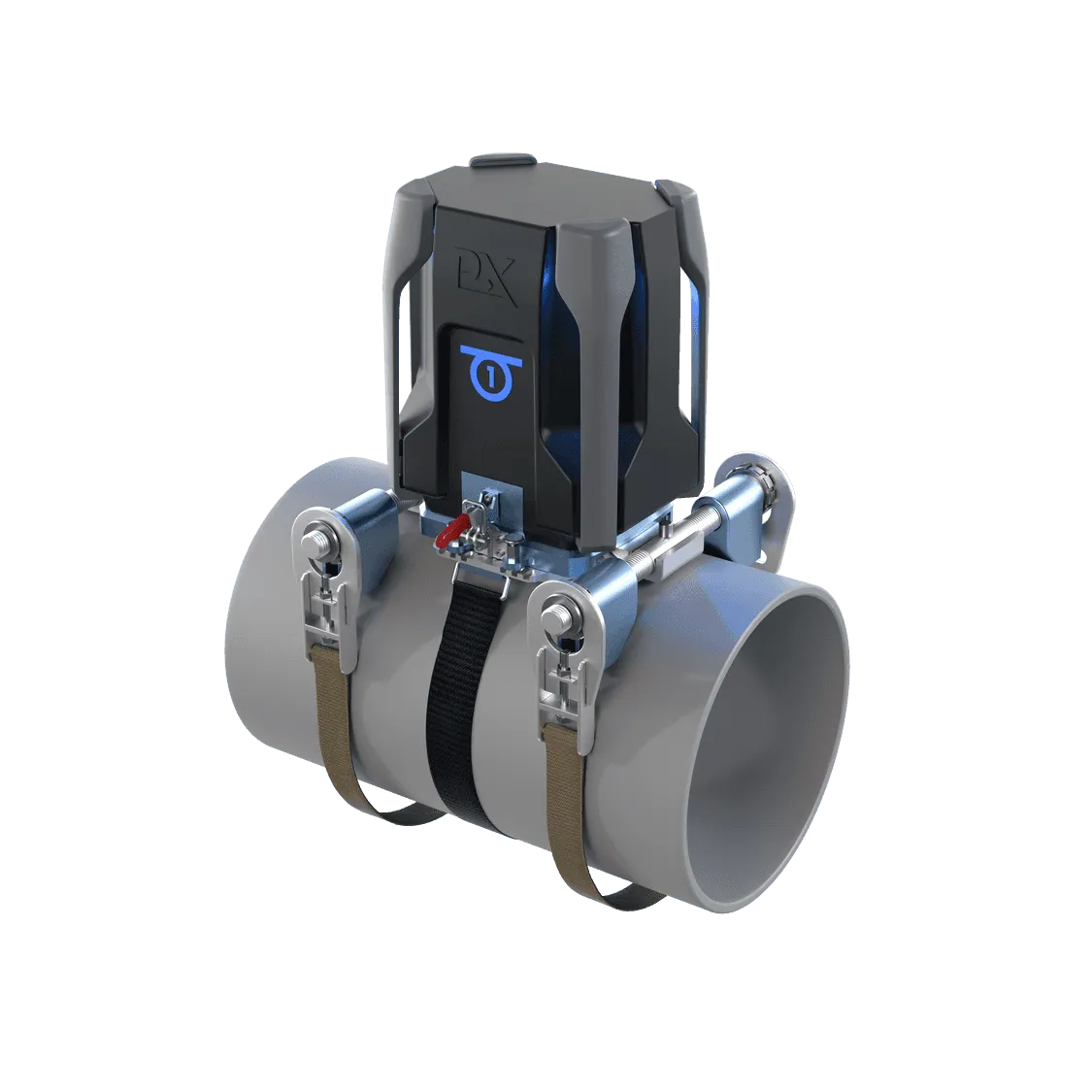
‍
Unlike the benchtop system, which uses a mechanical stylus profilometer, the portable system uses an optical profilometer that is based on white light interferometry, providing almost instantaneous access to the full 3D profile. After making software-driven corrections to account for pipe curvature and far-field tilt, the profile shape is analyzed in the exact same way that it is with the benchtop system (through an accelerated inverse finite element analysis). The portable PIP testing system is, therefore, a direct derivative of the benchtop system, deployed in a different testing configuration, but employing the same proven scientific methodology.
Minimal training requirements ensure large numbers of personnel can be trained quickly to use the equipment. Test results should be available for inspection immediately, with no finessing of the data needed following further, offsite analyses. The equipment is compact, robust, and easy to handle. It is also durable and can be carried in a technician’s truck as part of their standard equipment.
Mega Ruling
The “Mega Rule” presents a challenge to asset owners, asset operators and asset service providers that are involved with onshore steel transmission pipelines in terms of collecting or retaining traceable, verifiable, and complete (TVC) records that document material properties.
The “Mega Rule” was divided into three separate final rule actions, the first of which was published in October 2019. Part one of the rule requires operators of certain onshore steel gas transmission pipelines to reconfirm the MAOP of applicable segments – a perfect application for the PLX portable system.
“Quicker tests, using equipment that requires only one minimally trained operator can help support pipeline operators struggling with significant time constraints associated with the “Mega Rule.”
The “Mega Rule” further addresses material properties verification, the expansion of integrity assessments beyond high-consequence areas (HCAs), strengthened requirements for assessment methods, and other topics related primarily to threat evaluation and the assessment of risks.
The Clock's Ticking
The clock is ticking as PHMSA, citing existing requirements for collecting and using the data elements from ASME/ANSI B31.8S, has revised its final “Mega Rule,” appearing August 24, 2022, on the Federal Register. It states that operators must begin applicable data integration on the effective date of the rule—noted as May 24, 2023—and integrate all attributes within 18 months of this rule’s publication date. And herein lies the major challenge—time!
Part one went into effect July 1, 2021, setting expectations for pipeline operators to have a plan in place to verify MAOP, and requiring that 50% of that verification be completed within the first seven years—by July 3, 2028. The final “Mega Rule” affirms that applicable documentation must be maintained for the life of the pipeline and with the appropriate TVC records. If the relevant records necessary to substantiate MAOP are not TVC, the burden of testing and inspecting is shifted as operators must present their findings to PHMSA.
The final rule additionally stipulates that pipelines must be inspected within 72 hours following the cessation of extreme weather events, after the operator reasonably determines that the affected area can be safely accessed by available personnel and equipment. The urgency is real. Integrity assessments of pipelines will be required at least once every 10 years.
Beating the Clock
Quicker tests, using equipment that requires only one minimally trained operator can help support pipeline operators struggling with significant time constraints associated with the “Mega Rule.” From a testing perspective, the ability to scale up the appropriate technology quickly, and perform faster and more effective testing, aligns with what industry representatives are asking for. In fact, scaling up will be imperative to meet the testing needs across (potentially) a large number of digs in a brief period of time.
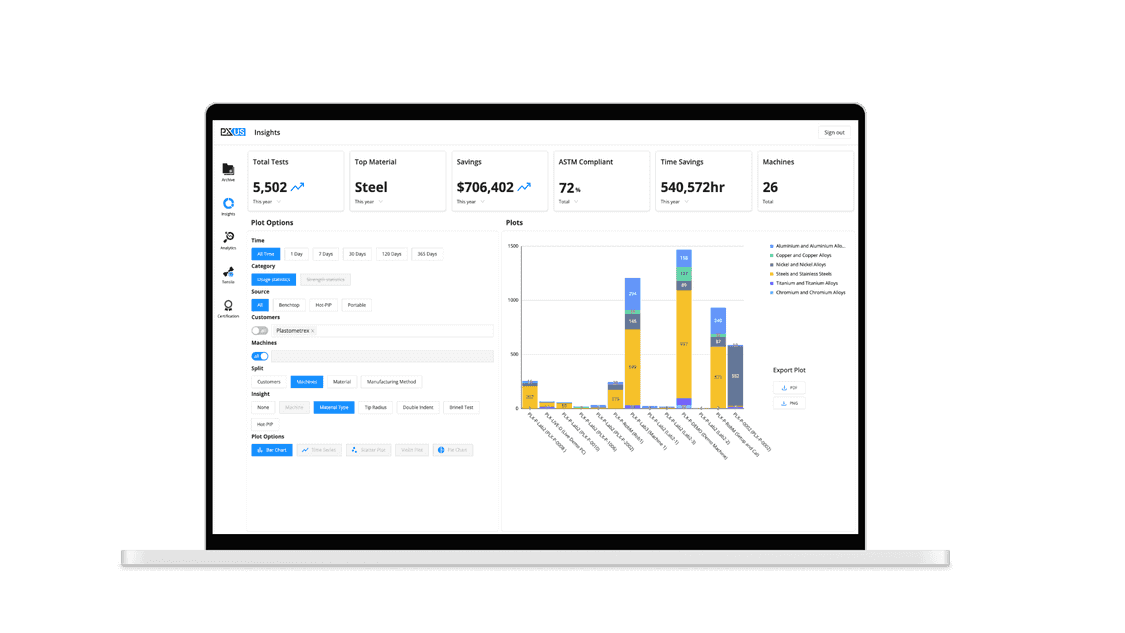
‍
What we are hearing at Plastometrex is that industry stakeholders do not want equipment that is too fragile, too expensive, or too hard to handle. In our view, the solution should be portable enough to carry in the rear of a utility vehicle, robust enough to withstand potentially harsh weather conditions, and practical enough to comply with the legislation. The business need revolves around safety, compliance, and efficiency. The faster the testing process (and the quicker the scale-up), the less time there will be wasted waiting for data to be compiled, uploaded, analyzed, documented, or acted upon. The portable Indentation Plastometer meets all such requirements, equating to less time in the ditch.
PLXUS - TVC Records Solved
PHMSA noted that, at a minimum, an operator should consider the same set of data on a periodic basis and analyze changes and trends that would indicate the need for additional integrity evaluations. For this to be feasible, results data should be stored in a centralized and easily accessible database that is compliant with the relevant regulations in the relevant jurisdictions. The over-application of assumptions in the absence of real data, PHMSA asserts, even if those assumptions are conservative, can lead to skewed or otherwise inaccurate risk analysis results.
On this basis, Plastometrex is developing its own digital platform (called PLXUS) for the automated collection, storage, and analysis of pipe testing data. This platform already exists for the benchtop device (Fig. 4), and is currently being extended to support PHMSA’s TVC record-keeping requirements. Like the benchtop device, results will be stored immediately in the PLXUS digital platform if a Wi-Fi signal is available, or stored locally until a Wi-Fi signal does become available. These datasets should therefore be available to colleagues that are off-site and/or in different locations, allowing real-time and in-ditch decision making. Over time, and with sufficient data, the PLXUS digital platform could be used to provide an overview of the health of the pipe network, to support reductions in overly conservative safety margins, and to support predictive maintenance scheduling.
Beyond the Mega Rule
Prolonging the life of the US gas pipeline infrastructure is critical from an energy security point of view, as is the ability of energy companies to meet growing sets of diverse energy demands. It’s perhaps even more important in this age of decarbonization and growing infrastructure demands, including those associated with the capture, storage, and transportation of hydrogen which will also require measurement and/or reconfirmation of material properties.
Collecting this data requires accurate and commercially viable testing processes and technologies that can be scaled at pace. Alternative technologies have already been proven too difficult, too slow, too expensive, and too inflexible to reach the scale required. However, portable PIP testing possesses all of the attributes that are needed for scalable, next generation non-destructive pipeline PMI.
‍