This blog post explores the complexities of metal plasticity, including how dislocations, grain structures, and various treatments affect a metal's yield stress and work hardening behaviour.
Overview of Metal Plasticity
Plastic deformation of metals most commonly occurs as a result of the glide of dislocations, driven by shear stresses. (In some cases, deformation twinning may contribute, but this also requires shear stresses in a similar way, and also involves no volume change.) In a polycrystal (ie in most metallic samples), individual grains must deform in a cooperative way, so that each undergoes a relatively complex shape change (requiring the operation of multiple slip systems), consistent with those of its neighbours.
It is not easy to study exactly what is going on inside a piece of metal while it undergoes plastic deformation, but there are some situations in which a picture can be obtained fairly easily. For example, Fig.1 shows an optical micrograph of the free surface around an indent (in a polycrystalline sample with a grain size of about 50 µm). This was originally a very flat (polished) surface, but after experiencing plastic strains ranging from a few % downwards (with increasing distance from the indent), it now exhibits a lot of surface steps. These arose from many dislocations following each other along particular slip planes (to create persistent slip bands). It can be seen that multiple slip occurred in most of the grains near to the indent. This took place while they all deformed in complex ways so as to create the overall deformation in the region concerned.
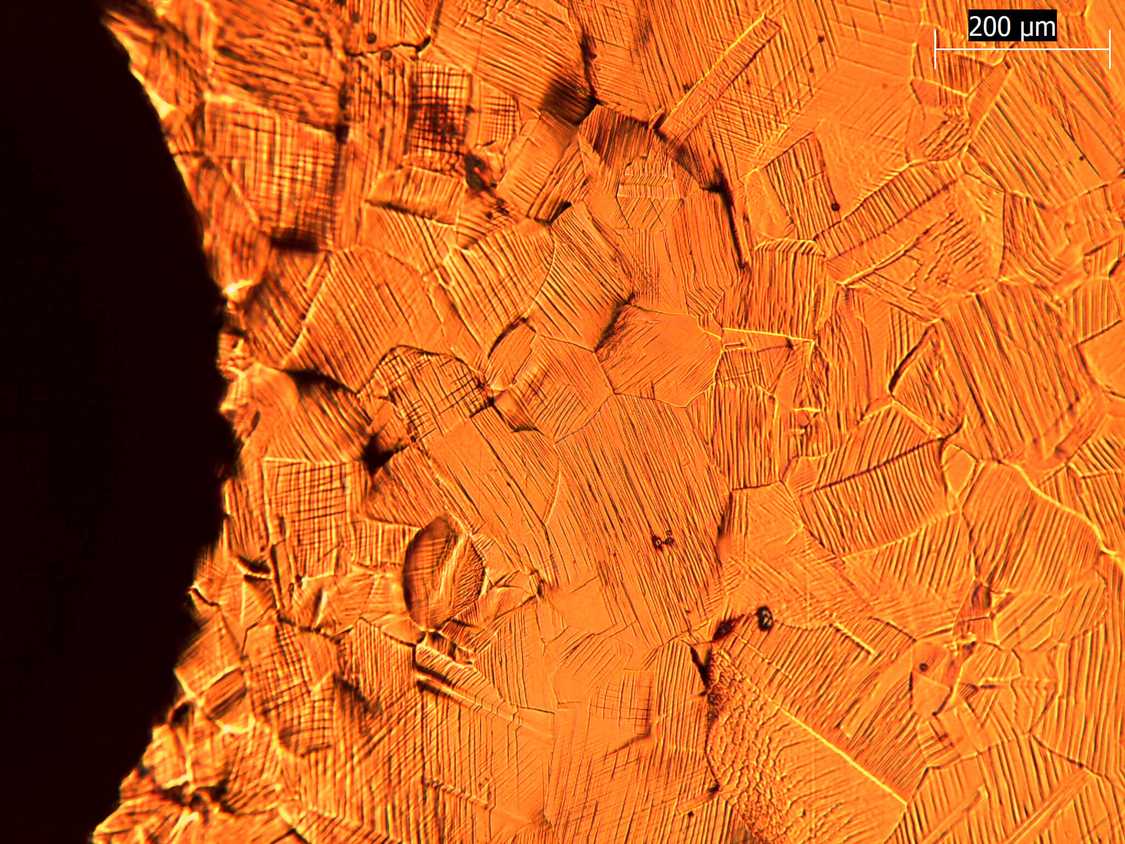
The Yield Stress and Work Hardening Characteristics
The (deviatoric) stress needed to initiate global plasticity in a sample is termed the yield stress. In general, continuation of plastic deformation requires a progressively increasing level of applied stress, apparent in a stress-strain curve (although this should be a true stress v. true strain plot in order to see exactly how the metal is responding). This effect is termed “work hardening” or “strain hardening”. It arises because, as more dislocations are created, and as they interact with each other (creating jogs and tangles), they tend to become less mobile.
The yield stress and the work hardening characteristics have a complex dependence on crystal structure, grain size, crystallographic texture, composition, phase constitution, grain boundary structure, prior dislocation density, impurity levels etc. Even for a given material, these plasticity characteristics can be dramatically changed by thermal or mechanical treatments or by exposure to various environments (chemical, irradiative etc). Accurate prediction of key mechanical properties of metallic alloys is virtually impossible, even if the microstructure has been carefully and comprehensively characterised. Such properties must therefore be measured experimentally, since they are of great importance for many (industrial) purposes.
The yield stress is usually taken to have a single value, but work hardening needs more complex definition. This must be valid over an appreciable range of plastic strain – perhaps 50% or more in some cases. Even metals that are relatively hard (and brittle) are normally required to have ductility levels (plastic strains to failure) of at least several % if they are to be used for engineering purposes.
Representation of Plasticity with Constitutive Laws
Of course, there is no expectation that the work hardening curve will conform to any particular functional form. However, in general, the work hardening rate (gradient of the true stress / true strain plot) tends to decrease progressively with increasing strain, perhaps eventually approaching a plateau. This is a consequence of competition between the creation of new dislocations, and inhibition of their mobility (by forming tangles etc), and processes (such as climb and cross-slip) that will allow them to become more organised and to annihilate each other. Initially, the former group of processes tends to dominate, but a balance may eventually be reached, so that the “flow stress” ceases to rise. (With metals, it is very rare, except with single crystals, for the work hardening rate to rise with increasing strain, although this is quite common in certain types of polymer, as a consequence of molecular reorganisation.)
Several analytical expressions have been proposed to characterise the work hardening of metals, but only two are in frequent use. The first is the Ludwik-Hollomon equation:
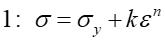
where σ is the (von Mises) applied stress, σY is its value at yield, εp is the plastic (von Mises) strain, K is the work hardening coefficient and n is the work hardening exponent. The second is the Voce equation:

The stress σs is a saturation level, while ε0 is a characteristic strain for the exponential approach of the stress towards this level.