In this blog post, we discuss how PIP works to determine a material's true stress-strain properties. The process involves making an indent on a sample's surface and analysing the resulting shape to extract this crucial information.
How does Profilometry-based Indentation Plastometry (PIP) work?
The PIP process (Profilometry-based Indentation Plastometry) involves indenting the surface of a sample and using the residual indent profile to determine a material’s true stress-strain characteristics. During indentation testing, the material beneath the indenter becomes strained, often over a very wide range of plastic strains, with the outcome being that the residual indent shape is very sensitive to the material’s bulk mechanical properties (primarily its plastic properties).
Additionally, the indenter tip has a diameter of the order of a couple of millimetres, and hence can deform multiple grains simultaneously to generate a bulk (polycrystalline) response. The Plastometrex software (CORSICA) uses iterative FEM simulation of the indentation process to fit a measured indent profile to the closest FEM-predicted profile, by iteratively updating the free parameters in a constitutive plasticity law (these free parameters being the yield stress and some hardening constants). A calculated nominal stress-strain curve can be compared directly to the data obtained from a conventional tensile test. An example of this is shown in Figure 1.
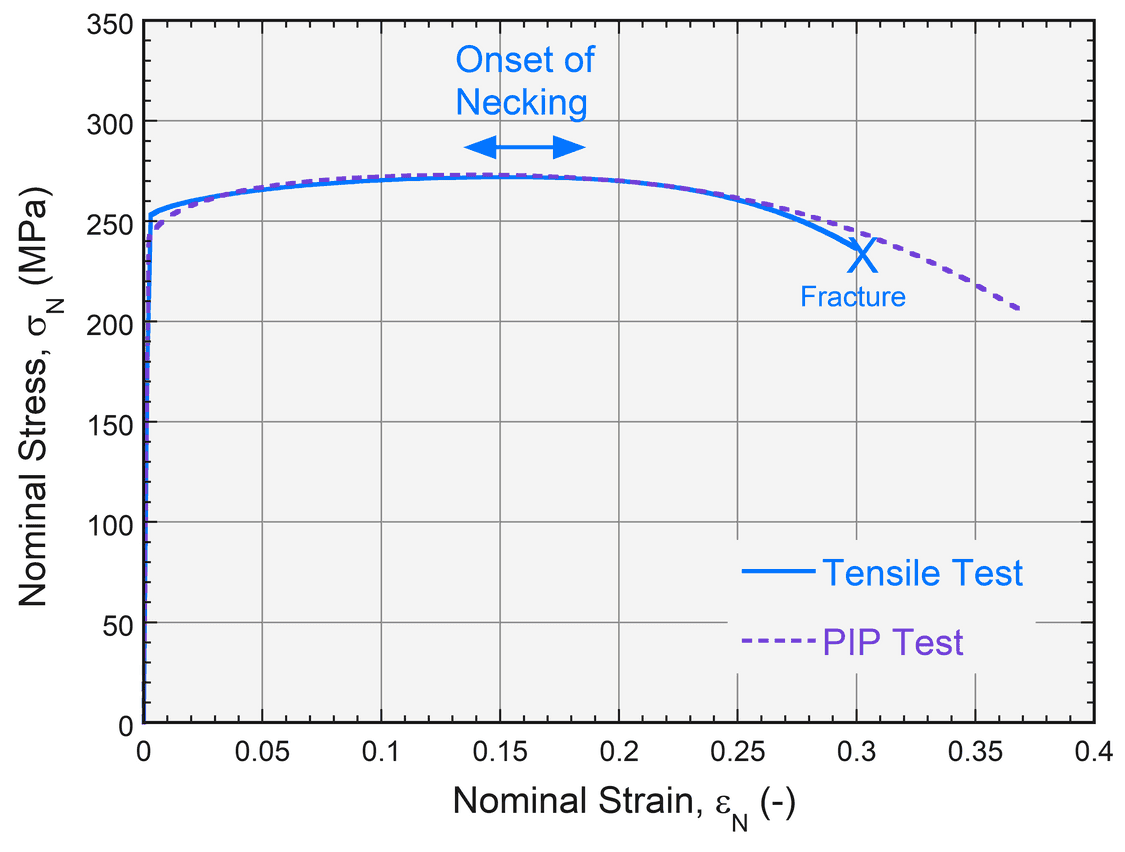
If PIP probes bulk properties of a material, why does surface preparation matter?
The residual profile shape is sensitive to the underlying strength characteristics of the material being indented. It is therefore important that the residual indent shape is measured with a high degree of accuracy. Large surface roughness levels have the potential to reduce the data quality by adding large amounts of noise to a profile scan (as seen in Figure 2).
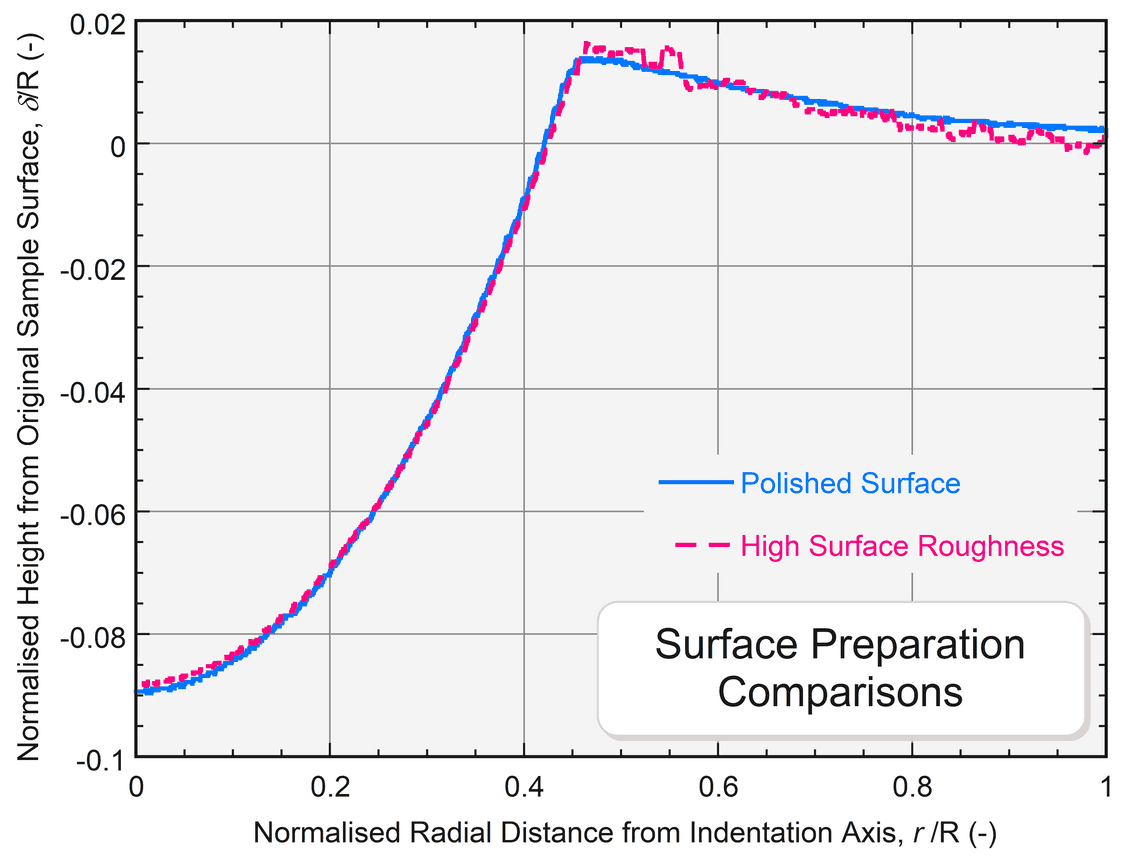
At Plastometrex, we have investigated how grinding a sample to different surface finishes affects the results obtained from PIP testing. This was done by preparing a sample using different grades (grits) of grinding paper (with a lower grit number meaning a higher surface roughness). We also tested highly polished surfaces. The indent profile was then measured both parallel and perpendicular to the grinding direction. From this study we can draw two main conclusions:
1. Changes in roughness in different directions (i.e. parallel and perpendicular to the grinding direction) were not detected above P400 grit.
A scan perpendicular to the grinding direction will show many bumps (from crossing in and out of the grinding scratches), whilst a scan parallel to the grinding direction may appear perfectly smooth (staying in a single scratch). Figure 3 shows that, with P120 grit paper grades, the peaks and troughs of the grinding scratches can be detected by the profilometer perpendicular to the grinding direction whereas, for P400 grit grades, there is no visible difference in either direction.
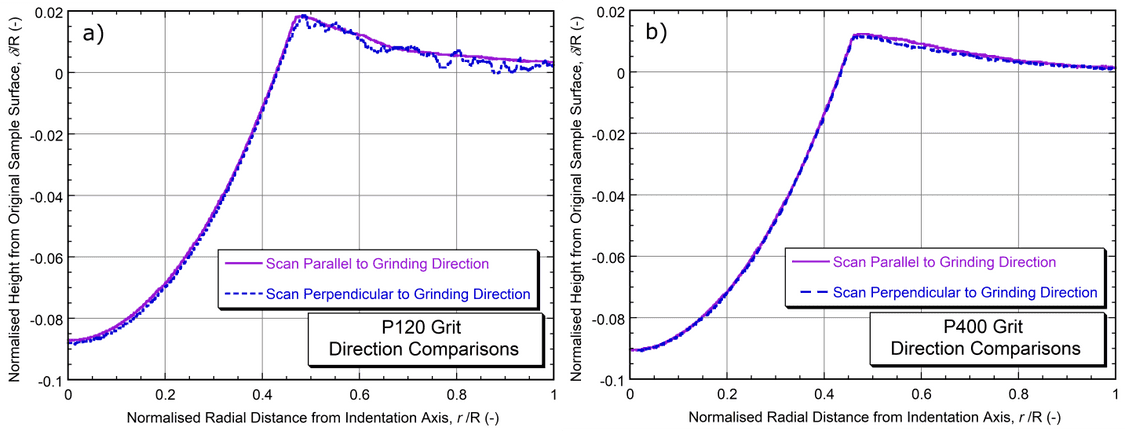
2. There is no systematic impact of surface roughness on PIP results above P400.
Studies on multiple metals did not show any systematic change of indent shape with different surface preparation above P400, and instead just demonstrated random scatter about a mean value. Different metals showed different levels of roughness, as softer metals deform more easily than harder metals and thus have deeper grinding scratches. This can be seen in Figure 4, where the aluminium and copper surfaces have higher surface roughness, Ra, than the steel and nickel surfaces at P120 grit. It is still important to prepare a surface to a high finish as this will mean the modelled profile from simulating the indent will match the measured profile more accurately, as the FEM model assumes a perfectly flat surface.
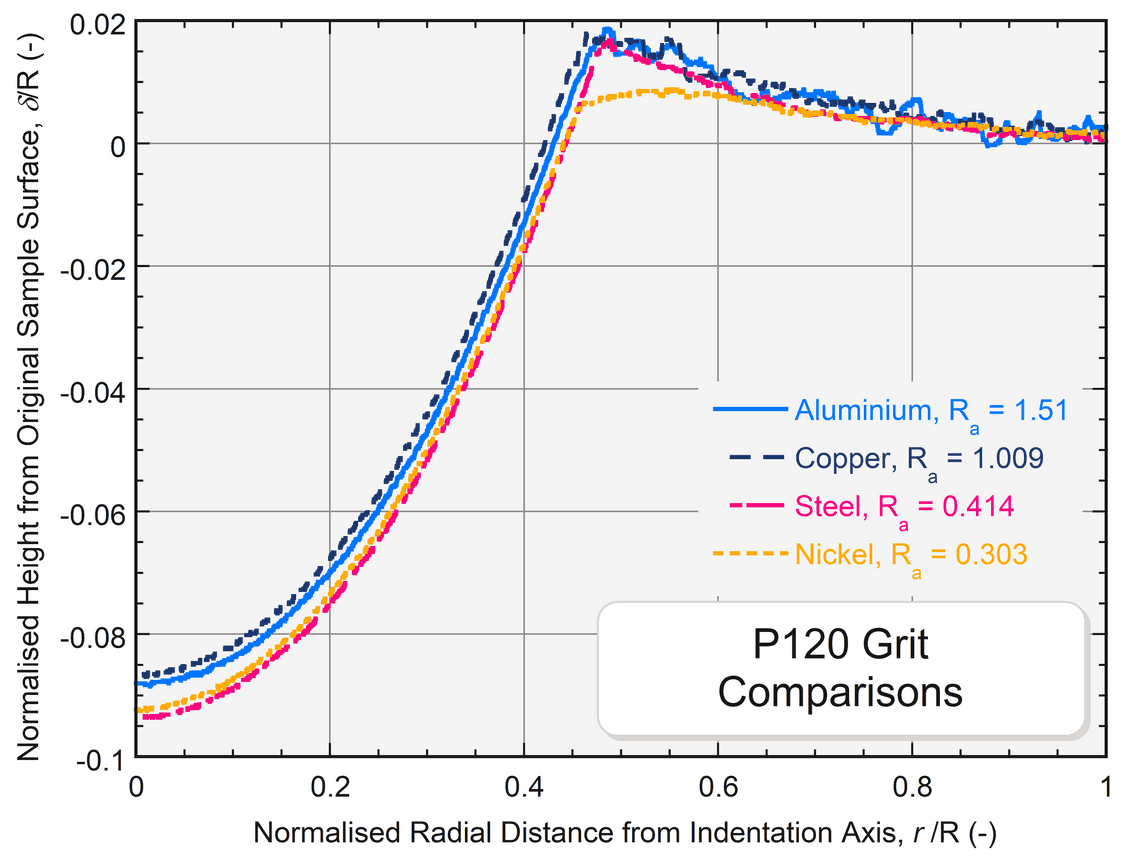
What does Plastometrex recommend?
At Plastometrex, we first recommend grinding samples to have two flat parallel surfaces, so the sample does not move during indentation and does not vary dramatically with height on either side of the indent (although our CORSICA software does apply tilt corrections for inclines of up to 2 degrees). We also recommend that the surface for indentation be prepared to P1200 grit, to ensure a good match between experimental and modelled profiles. Finally, if microstructural features such as rotated grains and persistent slip bands around the indent are going to be imaged, then it is recommended that the surface be polished.