In collaboration with 3D Systems, Plastometrex has explored the unique challenges of characterising multi-material interfaces in additive manufacturing. This study, presented by 3D Systems' Ryan Fishel and Tom Southern from Plastometrex at ICAM 2024 in Atlanta, Georgia, demonstrates how Profilometry-based Indentation Plastometry (PIP) can provide vital insights into material behaviour where conventional testing methods often fall short.
Overcoming Challenges in Multi-Material Additive Manufacturing
Multi-Material Additive Manufacturing (MMAM) offers transformative potential by combining dissimilar materials in a single component. This approach offers significant advantages, namely, reducing the number of components in an assembly and eliminating complex joining techniques. The benefits are far-reaching, enabling weight reduction and improved thermal performance, which are crucial for high-performance industries.
However, the interfaces where these dissimilar materials meet remain a critical area of uncertainty, posing challenges in both characterisation and performance prediction at both room and elevated temperatures. These interfaces are difficult to characterise with conventional testing techniques, including tensile testing, due to the spatial resolution required. Tensile testing can only give a single data point per sample, making it impossible to gather detailed information about the behaviour of materials near the interface.
This is where PIP shines. PIP testing offers the unique ability to derive stress-strain curves of the materials near the interfaces and examine the influence of different multi-material interfaces on bulk properties. Due to its ability to test on extremely small, complex, or otherwise hard to test samples, PIP can provide insights that traditional methods simply cannot deliver.
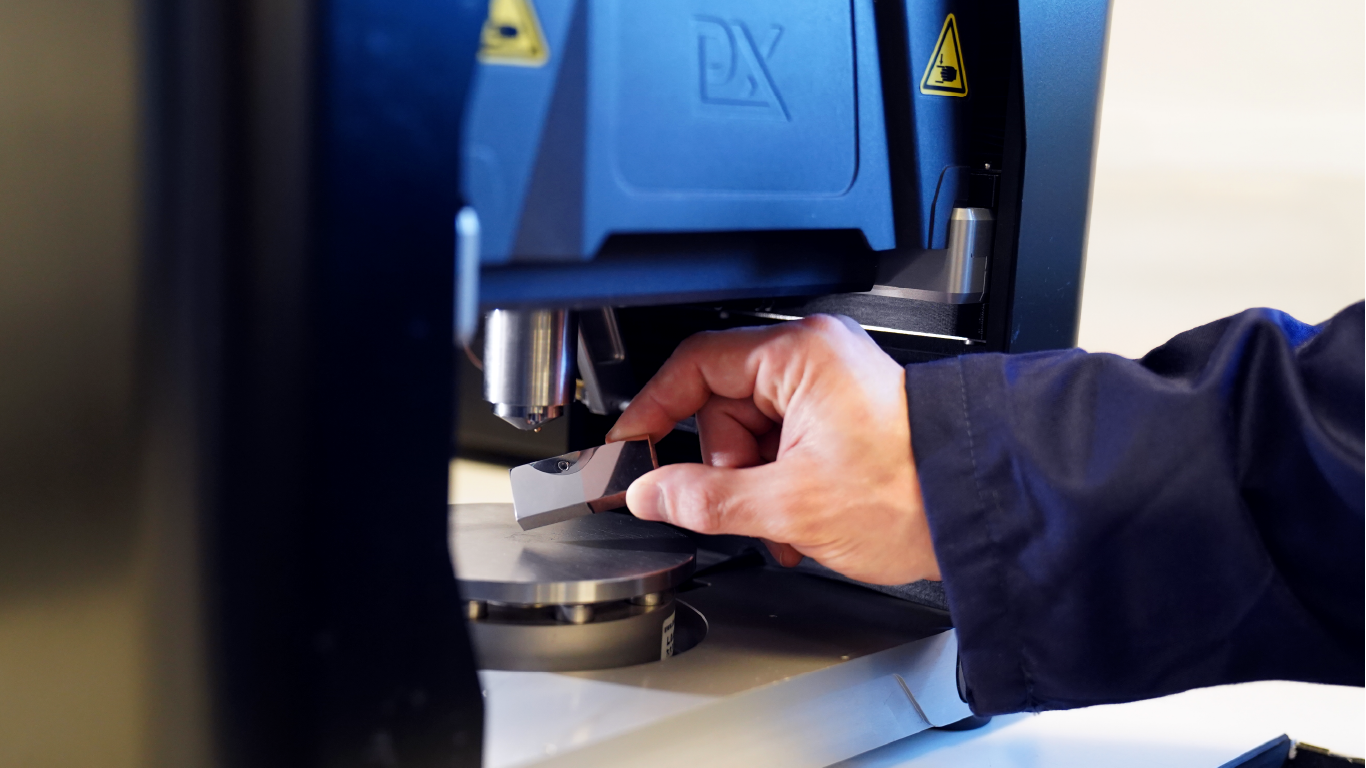
Case Study: GRCop-42 with Inconel 718 and 316L Stainless Steel
In our recent collaborative work with 3D Systems, room temperature PIP tests were performed on GRCop-42 + Inconel 718 and GRCop-42 +316L Stainless Steel using the PLX-Benchtop. For comparison, samples were tested in the bulk of each material (away from the interface) and near the interface within each material. This revealed key information about the effects of interfacial mixing on material properties.
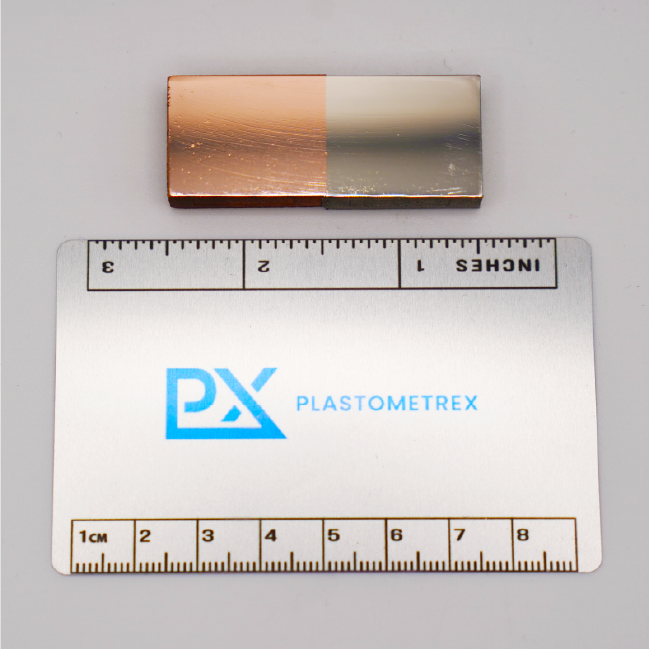
Electron microscopy results indicated greater mixing between GRCo p-42 and Ni718 than GRCop-42 and 316L. The PIP tests confirmed these findings: the GRCop-42 was strengthened more by its interface with Ni718 than with 316L, aligning with the observed mixing. It was further found that Ni718 experienced more pronounced weakening near its interface with GRCop-42 than 316L.
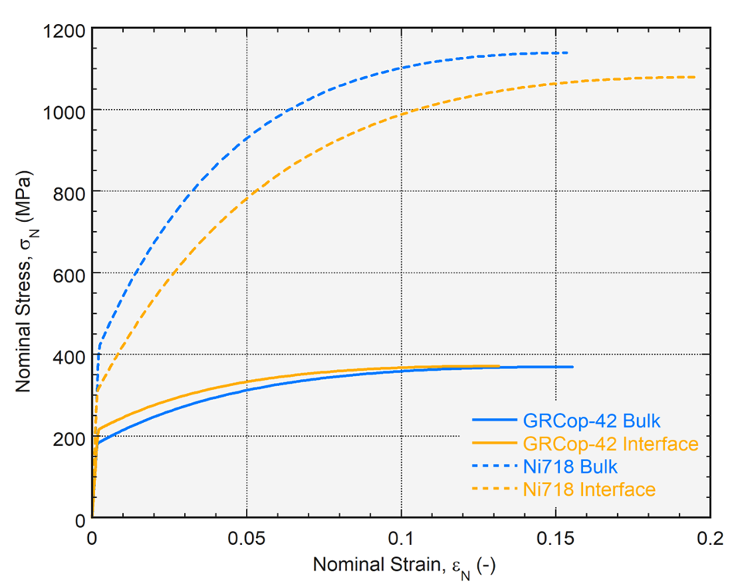
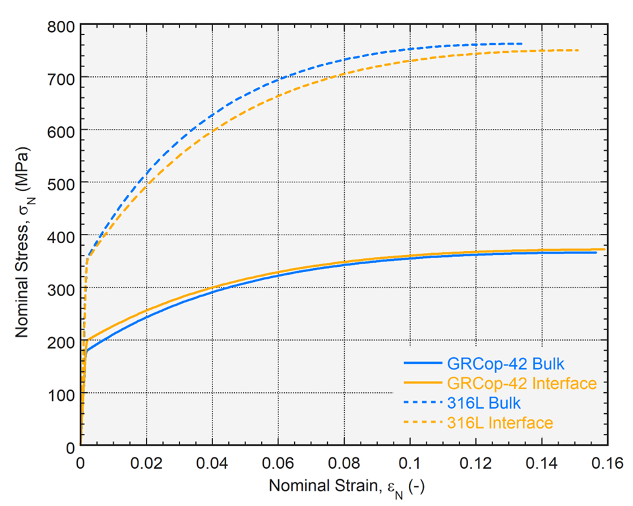
Given the target application of GRCop-42 as a high-temperature copper alloy, we extended our testing to elevated temperatures using the PLX-HotStage modular attachment, specifically at 760°C, on the GRCop-42 + Ni718 sample. This high-temperature testing provided insights into the behaviour of the interface under extreme conditions. As expected, the GRCop-42 experienced significant weakening at 760°C, while the Ni718 maintained its strength. This was clearly illustrated by the indent shape across the interface. GRCop-42 showed significant pile-up around the edge of the indent, indicating much lower hardness, whereas the Ni718 showed minimal pile-up, consistent with its retained strength.
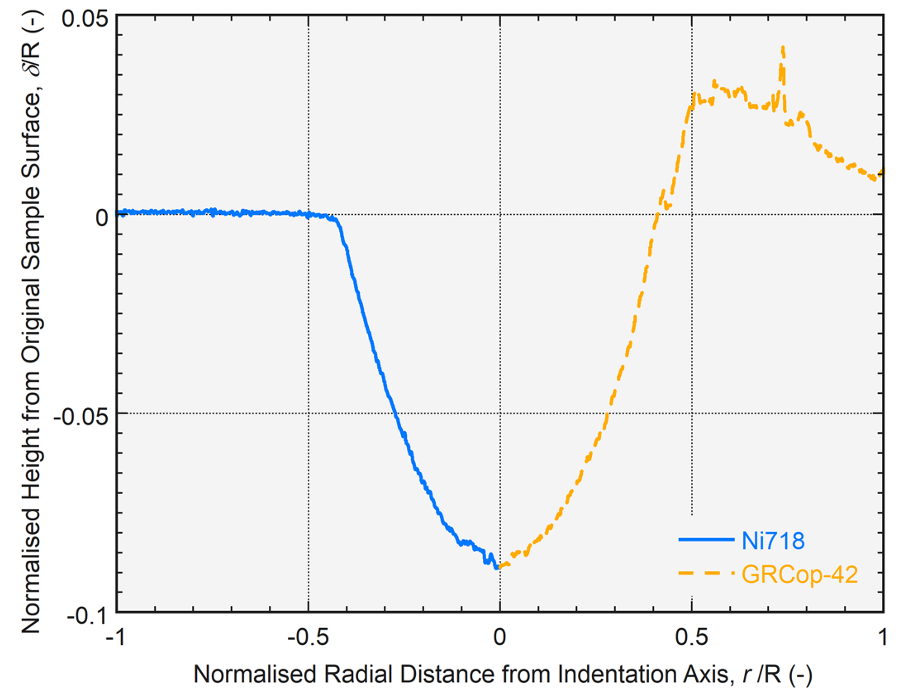
The Value of PIP in Multi-Material Analysis
Understanding material properties near the interface is crucial for the implementation of MMAM into part production. PIP testing offers vital, localised insights into how materials behave and interact at their interfaces. By linking the mechanical behaviour with the mixing of the materials near the interface, we can extrapolate the behaviour of other material interfaces. For instance, better mixing at the interface tends to strengthen the softer material while slightly compromising the strength of the harder material.
This ability to accurately characterise the properties of small, complex samples and test them under real-world conditions, including high temperatures, provides essential data for industries looking to adopt MMAM components. In sectors where material performance at elevated temperatures is critical, PIP testing can provide the necessary understanding to design and manufacture more reliable, high-performance parts.